Operational Excellence, OPEX, is an integral management philosophy which allows plant managers to maintain a focused eye on operating procedures and employee welfare, ensuring safety and efficiency. As such, OPEX must be recognized as the continuously-evolving system it is, based on checks and balances, to maintain improvement through people, processes, and technology. Key components of Operational Excellence can be applied to any number of industries, but let’s break down some of the integral parts of an OPEX system, specific to food manufacturing, and how well-defined programs attract the highest-quality candidates.
Committing to Excellence
Creating a system for Operational Excellence in food manufacturing will help to eliminate waste, streamline production, promote employee welfare and corporate culture, and ensure product quality control. A well-run, organized facility can expect the same quality in potential job candidates, especially with the assistance of staffing agencies who specialize in the industry. An informative article from LinkedIn expands upon of these concepts and more, but our list of indicators for implementing an OPEX program starts with a commitment to upholding standards of excellence and these key steps:
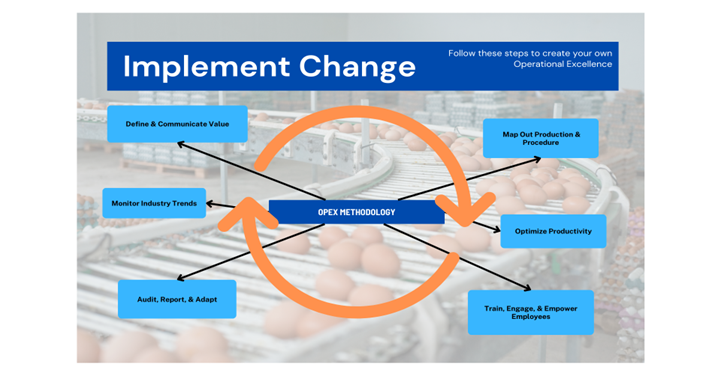
OPEX METHODOLOGY
Define & Communicate Value
While each manufacturer is different, you must identify and clearly define what products you assemble, what makes them valuable or sets them apart from competitors, and communicate that value to your consumers. Whether the differentiation be stringent food safety practices, innovative packaging, or operating a facility with an impressively low environmental impact – all of your unique offerings add value if you remember to communicate them clearly.
Map Out Production & Procedure
Understand and illustrate the entire process for manufacturing your products from raw materials to packaging and storage. Staying on top of your supply chain, cost fluctuations, and potentially problematic environmental or political impacts can help prepare for necessary changes if numbers come up out of range during report reviews. How each step of production is to be executed is just as imperative as knowing the path of materials. Creating, distributing, and displaying your facility’s Standard Operating Procedures helps to streamline production, keep employees safe, and uphold quality control through obvious and referable expectations.
Optimize Productivity
There are many pieces to this puzzle, but for this purpose we’re referring to your machinery and operating systems. In addition to routine audits to adhere to safety regulations, it’s important to check that equipment hardware and software are utilizing the most current features available and running smoothly. Machine hardware maintenance can prevent costly injury or potential contamination, which is a huge concern within the industry. Food safety starts with proper processes and sanitation. As far as software is concerned, updating regularly and maintaining frequency in reporting with exact specifications is helpful, and A.I. might be a great addition. Automated programmed reporting could help identify potential problems before they become issues, assisting the work of human operators and inspectors. This article published by the American Chemical Society CAS Science Team this past February goes into great detail about the benefits of incorporating A.I. into food production, especially how programs can reduce waste and escalate food safety.
Train, Engage, & Empower Employees
Safety first! Providing a safe environment for employees, including proper protocols and protective equipment is a must. But beyond basic regulatory requirements, complete and evolving training on equipment, processes, and product handling is also pertinent. Food production facilities are all unique, but commonly face some of the same challenges such as variables among age and physical capabilities of employees, experience levels, risk levels associated with machine operation, etc. Creating a system where your employees feel safe and educated, and also one that is inclusive and promotes communication, will attract the best candidates with the expertise and talent needed to continue positive growth. A safe, open workplace fosters increased individual production and instills a sense of pride in one’s work – which in turn, enhances output while also ensuring product safety. Additionally, it’s important to note that training is an ongoing art. Continued education, upskilling workers, improving human-machine collaboration, etc. are all facets of an effective OPEX system that help attract skilled laborers. The article “How to Build the Next Generation of Food Safety Leaders” article from Food Quality & Safety, Farm to Fork Safety, written by Patricia Wester, takes an informative deep dive into the importance of the employee experience in the facility and how to build future leaders.
Audit, Report, & Adapt
This step is a no-brainer, but still worth mentioning in our incremental indicators for OPEX. Understanding what reports to run to determine waste, loss of production, supplier price changes, etc. are all a part of Operational Excellence. While these reports will vary per facility/product, preparing a standardized list of frequently-reviewed audits will allow deeper insight into the lean manufacturing principles that will streamline workflows, improve overall management, and trim unnecessary costs. Start a baseline now, so future data can be compared to historic data and identify targets for change and new goals. Furthermore, adapting to change based on the results of those regimented reports creates opportunity for continuous innovation and success.
Monitor Industry Trends
Know your products and your market. Stay apprised of trends in the food manufacturing industry by following other businesses with similar offerings and learning about technological advances that can be applied to your facility’s specific systems – A.I. comes to the forefront again, here. Research and educate your management team.
Overall, Operational Excellence, and establishing a system to adhere to company and facility values – one which simultaneously demands the highest quality safety protocols, training, and employee welfare – will precipitate a response from highly talented candidates. In a nutshell, the more organized and safer your career opportunities are, higher rates of skilled workers will seek out careers within your business. Defining career paths from entry-level to upper-level management and projecting that information is enticing to professionals in the food manufacturing field. Understanding the knowledge awarded to us via these methods would suggest that creating dedicated positions specifically for OPEX officers is the next evolutionary step in the process. Titan Search is committed to aiding plant managers with this inaugural career path. With a pool of qualified candidates already in place, we can help merge the talents of these people with the needs of facilities – melding new positions created out of necessity with the skills possessed by many professionals in search of just a role. Even companies with the best practices in place could stand to initiate positions, and in turn, employees of those facilities may be enticed to help build these roles for others. As OPEX is an ongoing endeavor, it’s certainly worth the planning and execution, and deserves its own specified career path to further provoke positive growth, especially within the food industry.
Links:
- https://www.linkedin.com/advice/3/what-best-ways-implement-operational-excellence-rx9sf#:~:text=Operational%20excellence%20is%20a%20management%20philosophy%20that,improving%20processes%2C%20eliminating%20waste%2C%20and%20enhancing%20quality.
- https://www.cas.org/resources/cas-insights/digital-rd/embracing-future-ai-food-industry#:~:text=The%20application%20of%20AI%20in,and%20optimize%20supply%20chain%20management.
- https://www.cas.org/about-us
- https://www.foodqualityandsafety.com/article/how-to-build-the-next-generation-of-food-safety-leaders/
- https://www.foodqualityandsafety.com/
- https://www.foodqualityandsafety.com/author/pawester/
Additional Resources & Continued Reading